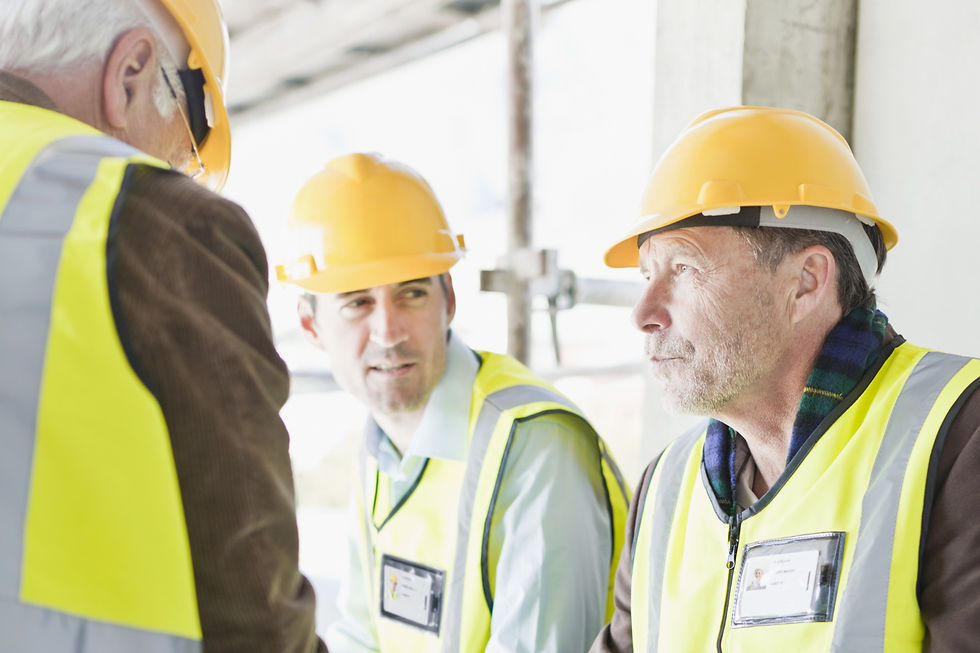
When controls don’t function properly, significant problems can arise at the most inopportune moments and send a project to a screeching halt. Many process controls projects are beset by problems that would have been foreseen had the work been performed by more attentive and qualified contractors. Choosing contractors wisely and following some important guidelines can spell the difference between a smooth, successful project and one that is fraught with problems.
Prequalify instrument contractors and system integrators. Find out what projects they have completed recently, and make the call to the clients to find out how they did. Ask about their strengths and weakness, and how they performed throughout the project, start to finish.
Provide bidders with a list of project details that are of critical importance to you and compare how much each bidder dedicates toward those items. This can indicate the seriousness of each contractor and how mindful they are to your primary project concerns, particularly instrument check, certifying networks, loop check, calibrations, startup assistance, etc.
Involve the bidders in document review and value engineering. Ask questions, and thoroughly evaluate the value of their input. Again, you can learn a lot about who has put serious thought into your project, and who is merely putting in a price.
Once you have a quality contractor on board, perform a full review of drawings and specs to avoid potential problems and leverage opportunity wherever possible. Experience should be valued, captured and implemented. Unless you’re in the business of fixing problems, you won’t know where they exist.
Make sure you purchase, receive, thoroughly inspect, bench calibrate, document and properly turn over all instruments in a timely manner. You don’t want to find out you have the wrong instrument at startup, and a replacement is 6-8 weeks away.
6. Get your contractor involved with planning locations of controls, indicating transmitters, control panels, and everything users and maintenance workers will operate and maintain. It’s important to make sure workers are satisfied with ease of use and access in the end.
Loop check and calibration should be a well-coordinated team effort, with the instrument contractor and system integrator working together toward a mutual goal. When problems arise, one team can concentrate on fixing the problems while the other team forges ahead.
Finally, have your instrument contractor get involved with the commissioning process. Their hands-on experience and knowledge can speed up commissioning and resolve technical issues on a variety of aspects of the project. Consider performing the first field calibration, as well. This can bring you to and through validation smoothly and successfully, rather than doing a last-minute scramble in the end.
About Omni
Omni Instrumentation & Electrical Services, Inc., located in New Jersey and Maryland, is a premier instrumentation and electrical contractor, providing superior total care solutions since 1986. Services include instrument installation, tubing installation, instrument calibration, control loop testing, startup and commissioning, power and lighting, process control wiring, BMS wiring, telecommunications and data wiring, fire alarm wiring, security wiring, process network wiring, and control panel fabrication. Omni Instrumentation & Electrical Services, Inc., is certified in Foundation Fieldbus, Profibus, DeviceNet and ASI-Bus installation.
Comments